5 Reasons Why PCB Manufacturers Reject Designs
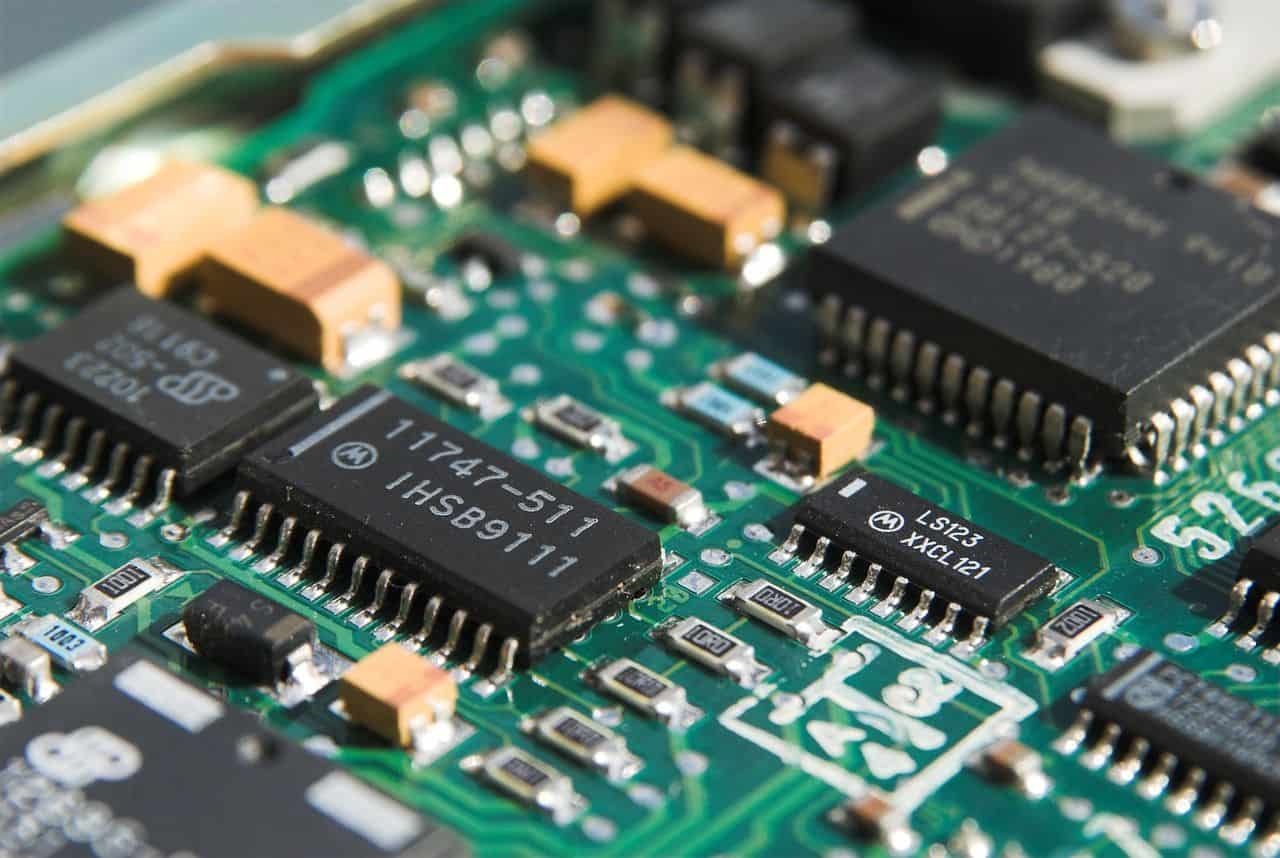
As a PCB designer, there can be nothing more disappointing than spending months working on a design to then have it rejected by a manufacturer. Of course, this does happen but there are usually important reasons why the manufacturing process cannot be completed. To help you avoid getting your design rejected, we have put together a list of some of the top reasons why a PCB manufacturer might reject your design.
No Class Type Indication
One of the first reasons why you might find that your design is rejected is that you have not indicated the class type that you are going to be using. In PCB board manufacturing this is very important and your manufacturer won’t be able to do their job properly if you have not indicated this. Make it clear if you are using Class 1, 2 or 3 to ensure that everything gets completed on time.
Poor Documentation
During the design process, you need to make sure that you are collecting any sort of documentation that might aid the manufacturer in completing the process. It is really important that you keep any files organized and keep a record of everything. Poor documentation can cause real problems so consider using a software package that allows you to generate this type of documentation as you go. Your manufacturer should be able to let you know what they require from you so find this out in advance.
Lack Of ITAR Requirements
Another reason why your PCB manufacturer might reject your design is that you have not properly inputted your International Traffic in Arms Regulations. For data packages to be handled properly this information must be included and they must be in the right location. If these are not documented properly, you will come across problems and your design might be rejected.
Missing Solder Specs
If you haven’t added details of all of your solder specs, then you might come across some more problems with having your design approved for manufacture. Think about the effect of RoHS regulations on your PCB design and make sure that your design is compliant. Let your manufacturer know if this does not apply to your design to avoid any sort of further problems during this process.
Lack Of Layer Sequences
The final reason why you might find that your PCB design has not been accepted for manufacture is that you are missing some of the vital layer sequences. Without this information, the manufacturer cannot create your PCB correctly as it is critical. Think about the number of layers in the copper image and lay it out in a logical manner. The more information you have the better if you want to get your design manufactured.
Follow our advice and avoid making these common mistakes to have your PCB design approved for manufacturing in the future. Not only will you save time, but you will also save some money on sending the design back and forth to the manufacturer.