Accurate Measurement of Temperatures In Industrial Processes Is Enabled by Technology
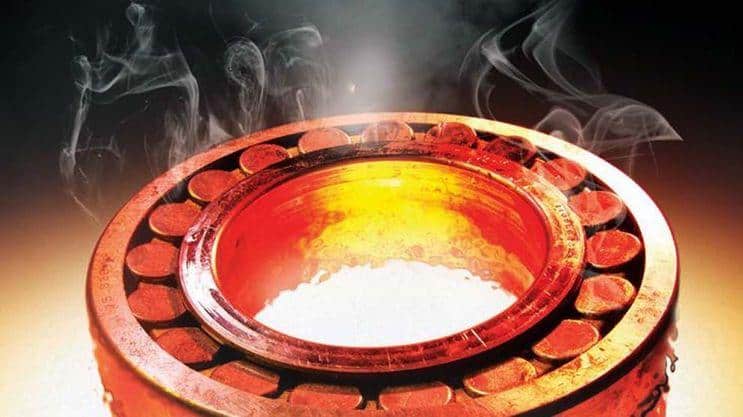
Many industries require precision in measuring temperature during their various production processes, and this requires temperature measuring equipment that is super sensitive and able to give the required degree of accuracy. Equipment for measuring temperature has led to great advances in the technology used and this allows them to provide information and temperature readings in the minutest detail. A lot of research has gone into these technologies that required a great deal of time, effort, and resources in order to take into account the needs and requirements of various industrial processes.
Temperature plays a large part in industrial processes and is for mechanical engineers a variable that is critical and needs an accurate measurement to decide the effectiveness of the processes used. During manufacturing, temperatures often required to be controlled or monitored. It can be as simple as knowing the temperature of water to knowing weld temperature in laser welding.
You may need to know the temperature of fluids in a process or the temperature of solid objects in a piece of machinery. Measurement of temperature in industries comes from a wide variety of applications and needs. The process control industry has developed technologies that use a large number of devices and sensors to satisfy this demand.
Temperature measurement can be either in the form of thermometers, probes or may be non-contact devices. Thermometers are part of the oldest technology that goes back many centuries, and today even the common man is familiar with glass tubes filled with mercury that accurately judge the body temperature, that is often an indicator of illness and disease.
These devices are not suitable for industrial processes where the range of temperatures that need to be read are very high. Process temperature measurement technology, therefore, makes use of many other methods for monitoring and measuring temperature.
Resistance thermometers are resistive thermal devices that use electricity to give very accurate readings of temperature. The temperature in metals leads to changes in their resistance and reading these changes leads to accurate readings. Most of these (RTD) resistance temperature detectors use platinum, but nickel and copper can also be used. These electrical temperature measuring devices can give you readings of processes that are over 1000 degrees Fahrenheit. These RTDs come in many different styles but the principle for measuring temperature remains the same.
Sensors are another development in technology that picks up changes in the temperature of the situation they are required to monitor. They have an advanced processing capability that allows them to transmit the needed information far more accurately than other devices would do. Thermocouples are the most widely used type of sensors and their low costs make them ideal for use in a vast variety of processes.
A thermocouple is made up of two different alloys that are connected at one end while the other end remains free. The voltage difference or EMF between the two open ends goes up as the temperature rises and is an indication of the temperature at the closed end. The open ends need to be at a standard temperature so that it becomes a direct function of the closed end temperature. This standard temperature is assumed as 0 degrees Centigrade and needs correction based on the actual temperature there. This correction is applied automatically in the instrumentation.
Thermistors are also durable and widely used sensors that have been developed for temperature measurements of processes. They are very accurate within limited temperature ranges. Thermistors use polymers, silicon or ceramic, and make for devices that are very small and relatively inexpensive. They are not as durable as thermocouples.
Electromagnetic energy is radiated from all matter, and in many process situations, this energy goes to the infrared region. A rise in temperature can increase the amount of infrared radiation leading to an increase in average frequency. Different materials radiate energy at various efficiency levels that are quantified as emissivity.
This emissivity is ranged from 0 to 1. Organic materials like skin have an emissivity of 0.95, while for polished metal, this can be twenty percent less. Infrared devices for measuring temperature take into account the emissivity of the surface that is undergoing measurement.
Other types of measurement devices that can be used in processes are bimetallic measurement devices, fluid expansion thermometers, and change of state sensors. Different metals expand at different rates, and when two metals are joined together, they will result in a distortion of their binding that is them mechanically translated into readings on a pointer. They are not as accurate as RTDs or thermocouples.
Fluid expansion thermometers use different fluids whose rate of expansion can be accurately measured and can also use gas. They do not require any power and are stable even after repeated use. Data from them is not easy to record or transmit. Change of state sensors is made from materials whose appearance changes at a particular temperature. They have low accuracy.
Selection of the right process temperature measurement technology depends on the accuracies and ranges required and the ease and economy of inserting these devices into the given process.