6 Easy Secrets To Cutting Labor Costs For Your Business
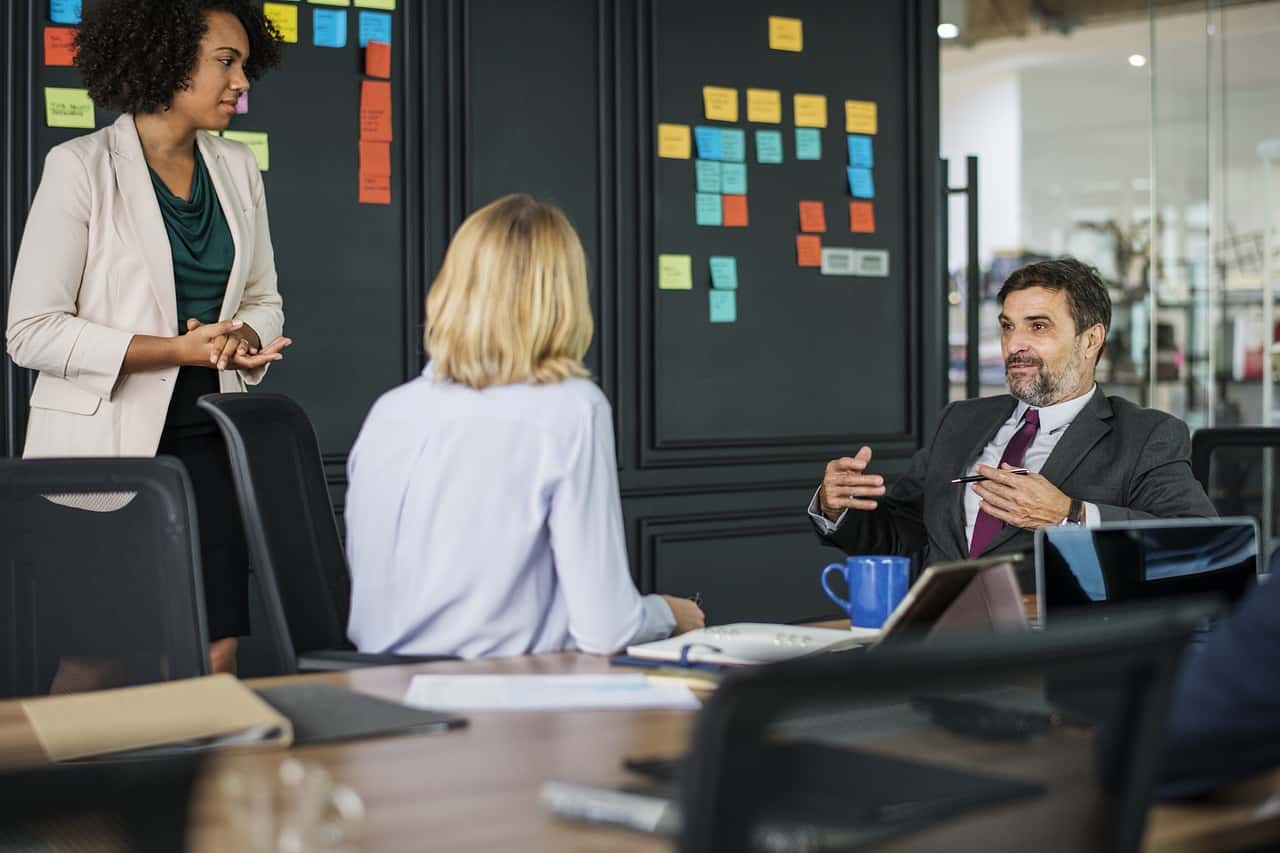
Wages and salaries are a major expense for any business. Yet they are essential to keep your operations running seamlessly. But uncontrolled labor costs can be a pain in the neck for any organization. They can topple your budget and reduce the overall profitability. Keeping them under control, therefore, should be your top priority. What can you do to reduce these costs? Is it feasible to layoff the employees or suggest a wage cut as cost-cutting strategies?
These will probably do more harm than good as you will end up with an unhappy and dissatisfied workforce. They will not contribute and may even consider leaving for good. It would be better to take a more positive approach to bring down labor costs. Proper workforce management strategies can play a key role in ensuring that you spend an optimal amount on the wages. Here are some secrets that can be helpful for cutting labor costs to a considerable extent.
Evaluate and streamline processes
Faulty processes are one of the main reasons for high labor costs. Employees fail to do their jobs quickly and efficiently in the absence of proper processes. You need to evaluate the processes for identifying the loopholes and bottlenecks in them. Find the gaps and address them by streamlining the processes. This will automatically bring down labor costs and maximize their efficiency and productivity as well. For example, you can start using production automation tools to reduce the dependence on labor and decrease the error rate.
Ensure painless scheduling
While process optimization is important, proper scheduling is equally vital for bringing down the labor costs for your business. Ensure that you allocate the right tasks and shifts to the right employees. If people are made to work according to their preferences, they tend to contribute more. Proper scheduling also ensures a smooth workflow through shifts. It minimizes the chances of over-staffing and under-staffing, which means that there is no wastage or shortage of resources.
Invest in technology
Investing in technology is a smart move if you want to cut down the labor costs in the long run. You can start using advanced equipment to substitute labor for repetitive and time-consuming jobs. Similarly, process management software solutions make a good investment. For instance, you can reduce wage costs with this scheduling software which also serves as a smart communication tool. Such applications reduce the burden on the managers by automating the entire scheduling process. They can prepare schedules in minutes and share them with the employees as well.
Avoid overtime
Overtime is a practice that can increase your labor cost to a significant extent. This is because you need to pay considerably more than the average hourly rate to have people give in extra work hours. Avoiding overtime is a good strategy if you want to save on this extra cost. Consider alternatives such as part-time hiring during the high-demand periods. This enables you to overcome the labor gaps without having to hire resources that are not needed otherwise. Extended shifts and shift swaps also work if you want to avoid overtime costs.
Reduce employee turnover
High employee turnover increases your business expense in terms of recruitment, onboarding and training new staff. Moreover, it can add up to invisible costs such as poor work quality, wastage and longer production hours. If you really want to save up on these expenses, make efforts to maintain a stable employee core. Work on building a highly satisfied workforce that wants to stay with your organization in the long run. Focus on allocating tasks according to their skills and give optimal time offs to ensure physical and mental well-being. Training your staff to enhance their skills is another good idea.
Monitor labor costs
Keeping an eye on the labor costs is essential if you want to cut them down. The idea is to find the gaps and areas that are making the costs rise. Managers should compare the theoretical costs with the actual ones. Unless you know where you are lacking, you will not be able to address the areas. Further, monitoring can also help managers to forecast future costs and plan what they can do to control them.
Excessive labor costs can be a killer for any business. Lowering them, therefore, should be a part of your long-term strategy. Look for effective solutions that improve the overall efficiency of that labor rather than just limit costs. Remember that your workforce is an asset and not a burden for your business. Empower them with the tools that they require to drive efficiency and reduce costs to boost the growth of your business as a whole.