Why Using CAD/CAM in the Sheet Metal Fabrication Industry Is Beneficial
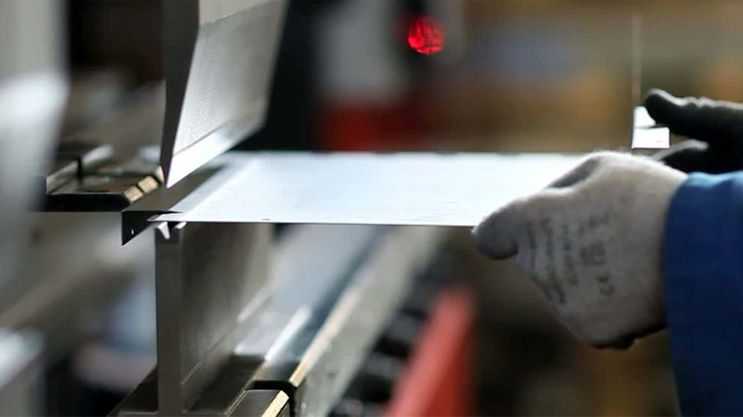
For decades the sheet metal fabrication industry relied on 2D drawings to design and cut the essential parts. But the advent of 3D CAD workflow has outweighed the 2D technology in every aspect. Whether it is profitability or productivity, 3D CAD is the way forward as it opens up countless opportunities for the sheet metal fabricating business to flourish. Beyond the opportunities provided, there are also cost benefits from cost estimation in 2D drawings, 3D cad models that Galorth can help provide.
Wondering why it is making such a difference? Here’s everything you need to know.
Better Designs
Probably the most crucial benefit of using CAD in this industry is for its design capabilities. With an improvement in overall design quality, accuracy, and reduced scrap, this technology is way ahead of its predecessor. Some of the CAD modelling tools also come with sheet metal features that allow the designers to design a complete product like it would look once it is manufactured. You don’t need to design and assemble parts to understand the complete structure of the product.
With only a few mouse clicks, you can now flatten the entire sheet metal object, including all the allowances so that performing sheet metal operations are easier. This is a massive upgrade from the previous CAD versions because it saves a lot of time both for the client and the designer. Also, with improved visibility, the engineering team can quickly communicate the changes in the design if any, with the non-technical staff so that everyone is on the same page. Clients these days want quotations along with a 3D model, and this technology helps deliver precisely what the clients desire.
Improves accuracy and drafting quality
The modern CAD technology has parametric capabilities. It means if the sheet metal requires any change in the model, the edits will automatically reflect in the 2D drafts used in the shop floor. Previously, designers had to tally everything manually if the sheets needed any changes. The introduction of parametric capabilities eliminates the inconsistencies in the overall design communication. They also offer better controls over the other versions of the design.
3D CAD/CAM is a boon for the sheet metal fabrication industry. Its accuracy in the workflow provides much-needed confidence to the teams that helps in efficiency and also improves productivity in the development process.
Virtual test design
3D CAD models, together with defined physics such as flow or load conditions, pressure, or temperature, are some of the factors that the simulation tools require to test the efficiency of the product. This approach is not only a massive cost-saver but also reduces the time to perform physical tests. Their efficiency allows the sheet metal fabricators to come up with high-quality products that usually market faster.
Develop better marketing materials
Many modelling tools allow sheet metal parts to convert to 3D CAD models giving valuable insight to the designer during the design process. Similarly, there are tools and plugins that you can use for woodworking and other products.
Automate designing of configurable products
With 3D CAD workflows, countless possibilities can improve the metal sheet fabrication business. It takes productivity to the next level by merely implementing design automation. Fabricators who are involved in developing configurable products like windows, doors, conveyor systems, cabinets, etc. can now automate repetitive tasks like drawings, documentation, and even generating customized 3D models.
Companies that are already using design automation are in full support of this system. They share that this technology reduces lead times by as much as 50%. Plus, they have gained competitive differentiation as they could deliver customized products quickly and efficiently.
Why CAD/CAM is the future
Back in the 1960s, experts tried to tweak the drafting procedure and make it automated, but the technology was not so advanced, and that is why 2D fabrication was the only choice that sheet metal fabricators had. However, modern-day manufacturers use the 3D model to fulfil various purposes. Since you can magnify the model, it eliminates the risk of making a mistake in the design process. It also allows you to rotate the model in every axis you want. This gives a manufacturer a better sense of the product and how it might look when it is complete. Merely designing a product based on assumptions, and then making significant changes is not a practical idea anymore.
Apart from all these benefits, CAD also simulates the movement of the parts during the production process. For example, it can simulate speeds of tooling, feed rates, positioning of the clamps holding the part, and various other factors that usually limit the machine’s efficiency. They also assist in the programming of the machine as you can import the files into the software application. This speeds up the programming process so that you have time to make any changes if the client wants.
Designers and engineers involved in the sheet metal fabrication industry are in awe of the latest CAD modelling tools. Their efficiency is unmatched, and with the planned upgrades, it seems CAD/CAM is the future of this industry for years to come.